Efficient industrial operations are the cornerstone of any successful manufacturing or production business. By optimizing processes and taking proactive steps, plants can maximize output while minimizing costs. Sound maintenance, modern automation, rigorous safety standards, adept supply chain management, and data analysis are all critical components of a smooth operation. Below are some tips on how to achieve that. Keep reading to explore these foundational strategies in more depth.
Implementing Strategic Maintenance for Industrial Equipment
For industrial equipment to run reliably, a strategic maintenance plan is vital. This involves regular check-ups and the replacement of worn parts before they lead to breakdowns. By adopting a schedule that aligns with the manufacturer’s recommendations and the real-time data from usage, unexpected downtime can be reduced significantly. This balance ensures that while maintenance is ongoing, it isn’t so frequent that it incurs unnecessary costs or downtime.
The introduction of condition-monitoring tools can take maintenance a step further. These tools identify potential problems before they become serious, allowing for the timely scheduling of repairs. Sophisticated refrigeration equipment such as industrial ice makers, which are critical in food processing and chemical industries, require vigilant maintenance programs to ensure continuous and safe operation.
Adopting advanced tracking systems, like COI tracking, also helps in monitoring a certificate of insurance. Moreover, risk management platforms automate the verification of insurance, licenses, and compliance docs—reducing business friction and enhancing trust.
You may like – The Importance of Data Centralization for Business Success
Embracing Automation To Enhance Efficiency
Automation in industrial contexts has revolutionized how businesses operate. Incorporating automatic processes reduces the strain on human workers and can improve precision in production. Automated systems often complete tasks more quickly and with fewer errors, leading to an overall increase in productivity.
However, the implementation of automation should be considered carefully. Assessing which processes would benefit from automation and to what degree is important, as this technology represents a significant investment. A step-by-step approach may be ideal, starting with the most repetitive, time-consuming tasks that are prone to human error.
Moreover, automation can help in gathering precise data regarding the manufacturing process. Sensors and controllers can provide real-time oversight, allowing for immediate adjustments and reducing waste. It also fosters a safer work environment by delegating risky tasks to automated systems.
Fostering a Culture of Safety in the Workplace
Safety is paramount in any industrial setting. Creating a culture of safety that prioritizes the well-being of employees is not only ethical but also economically sound. Safe work environments reduce the risk of accidents that can lead to costly downtime and liabilities. It starts with comprehensive training and a clear understanding of safety protocols for all staff members.
Regular safety drills and access to up-to-date safety equipment are necessary to prepare for any emergencies. Consistent communication regarding safety measures and the encouragement of safety recommendations from staff can lead to a proactive safety culture. An empowered workforce takes ownership of safety practices.
Leveraging Data Analytics for Operational Insights and Continuous Improvement
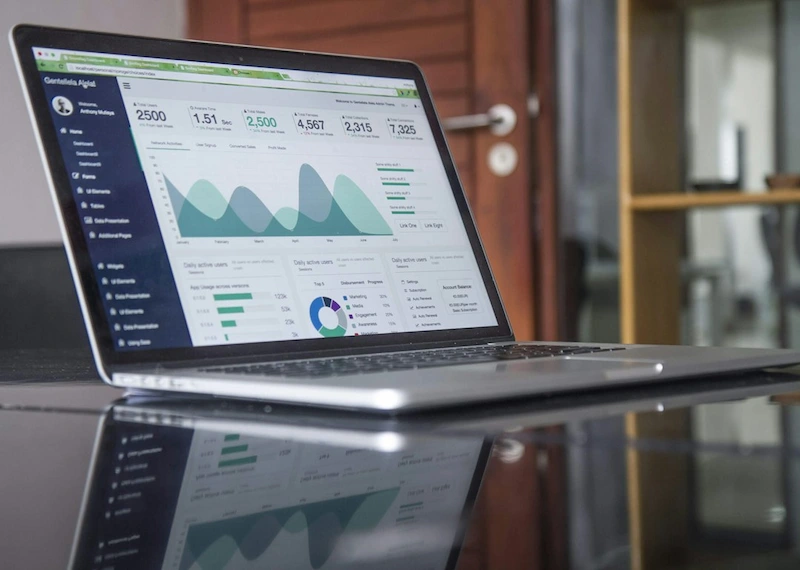
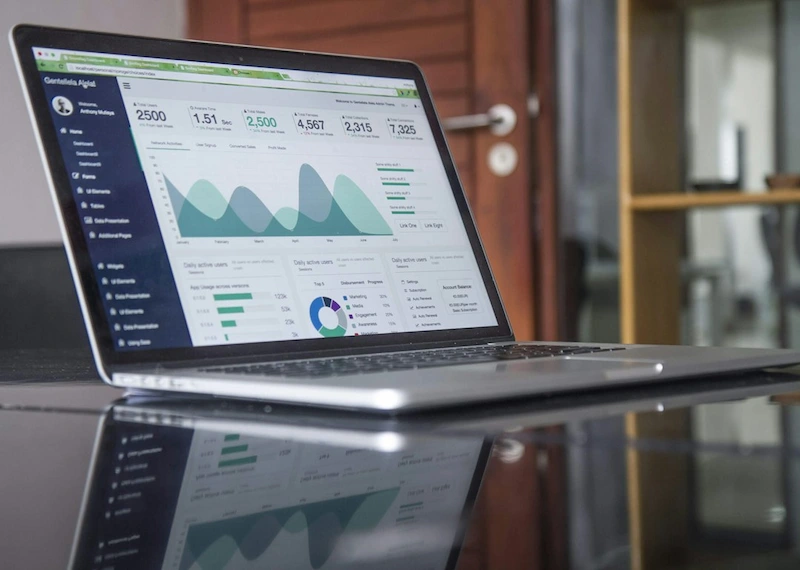
In the age of Big Data, industrial operations can gain significant advantages by leveraging data analytics. This capability allows for the extraction of meaningful insights from vast data sets to inform strategic decisions. By analyzing trends and performance metrics, organizations can pinpoint areas for improvement and investment.
One application of data analytics is predictive maintenance, which can prevent equipment failures before they occur. By analyzing performance data, it is possible to identify patterns that precede failure, allowing for timely maintenance and repairs. This approach ensures maximum uptime for crucial machinery and equipment.
Altogether, running a smooth industrial operation entails a synergy of strategic maintenance, embracing advancements in automation, fostering a steadfast culture of safety, and leveraging big data for insightful decision-making. These practices contribute to creating a resilient, efficient, and progressive industrial environment, ultimately driving success in an ever-competitive marketplace.